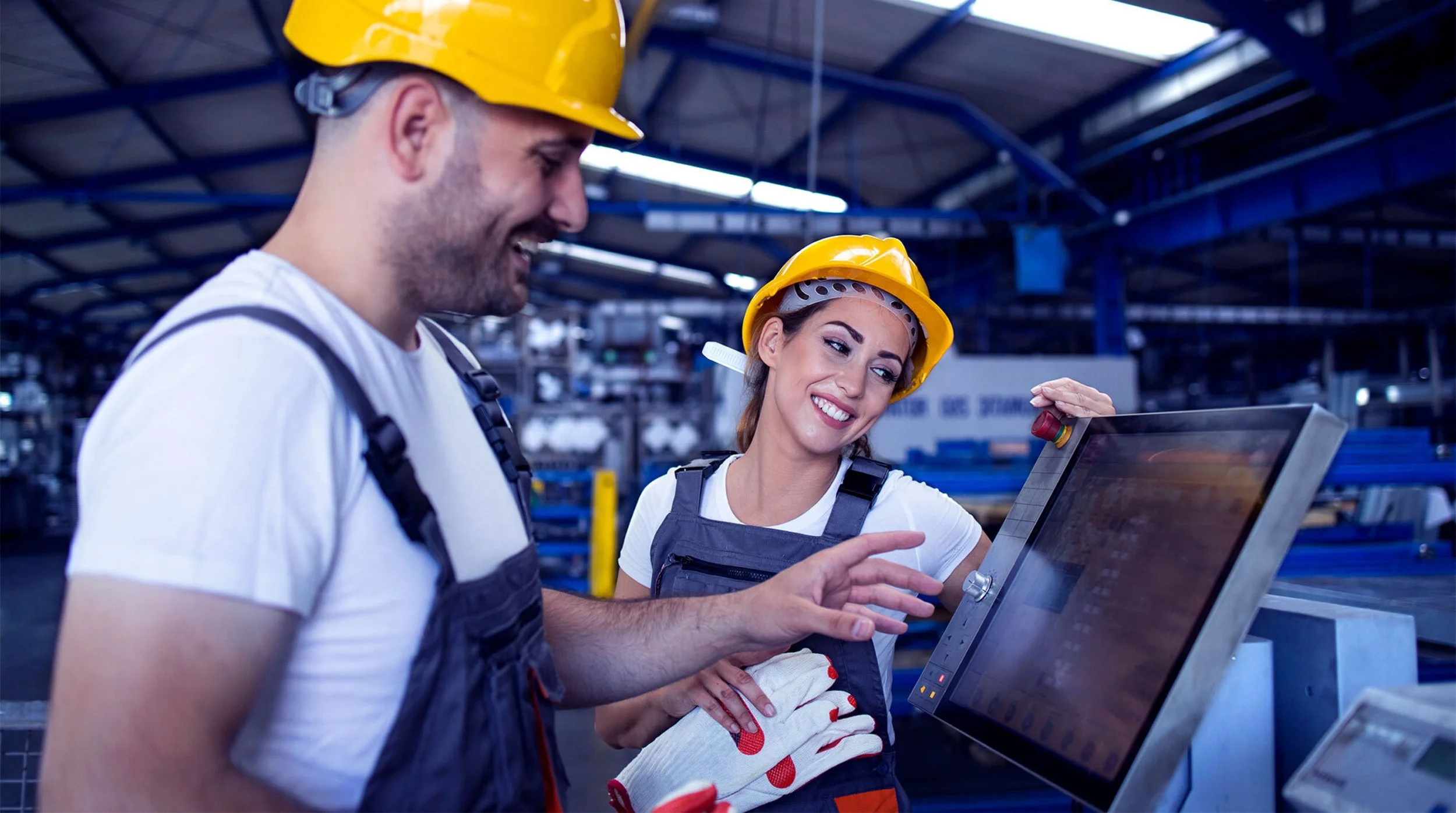
Machine Monitoring Application
The ask was to design and develop an end-to-end industrial domain machine monitoring solution with special focus on Original Equipment Manufacturers.
Client
Rockwell Automation, United States
Project Duration
31 weeks
Responsibilities
Program Planning, SME & Stakeholder interviews, Competitive Benchmarking, Wireframes, Rapid prototyping, Visual Designs, Usability Tests, Visual Design QA
Process
Within 7 weeks of foundational research, we interviewed 7 stakeholders and 7 SME’s to identify the key users, their goals and pain points in order to come up with a design solution that would allow OEM’s to set up their own monitoring system without the need of consulting third party experts.
We created close to 20+ design flows, integrating new technology and processes while using existing conventions to streamline the experience.
All the concepts were prototyped, implemented and tested with 7 SME’s. Based on which, selected design flows were refined, each representing opportunities for improved user experience.
Challenge
Since, this was the first time we were going to work in the IIOT domain, we struggled to grasp the technical terms because they covered such a broad variety of terminologies and issues. Everything became visible as we began undertaking primary research. Everything started to fall into place as things became clear, and we defined the service blueprint.
Approach
Following the completion of the original study, we began conducting competitor reviews and synthesizing insights in order to develop personas. We proceeded by building the IA’s, followed by high level conceptual flows and parallel doing the visual explorations.
Immersion
Personas
User: Admin
User: Engineer
User Journey
Information Architecture
Insights
Configuration Complexity
The current IIOT solutions are fragmented, very tedious, time-consuming and difficult to configure. It comes down to our users to figure all of this out. A lot of the tasks are currently manual, such as searching and assigning sensory data tags. These tasks tend to be time-consuming, often repeated at different levels.
The IOT Gap
Most of our customers have great industry expertise but lack the know-how to transition into a cloud based model of working. The current solutions expect them to do a lot without connecting these dots.
High Downtime Cost
Most of the time when machines are not working, the downtime cost is very high, and it comes down to the OEMs to pay for it. Due to lack of remote monitoring, OEMs are unable to identify the problems which leads to financial losses to them.
Competitor Analysis
Discovery
Outcome
Based on stakeholder & user interviews, competitor analysis and key insights, we brainstormed on wireframes, and detailed high-fidelity mockups. We also conducted usability tests with SME’s to get early feedbacks and incorporated the same into our designs. In parallel the visual designs were also picked up by the team members.
Deliverables
We delivered a comprehensive set off research insights and competitor analysis along with working design wireframes, final visual designs and a style guide for reference.
Furthermore, frog has provided a technical documentation addressed to developers in which all the visual design analysis have been thoroughly investigated in detail as a handover to development.
Results
Making IIOT Simple!
Thanks to the functional and impactful frog approach, the new design provided can be easily declined on all types of devices, returning a simple and frictionless user experience.
Reduced Human Intervention
The new product reduces considerable human effort by automating manual tasks and using Rockwell’s intellectual expertise to create a library of templates, thereby considerably reducing the time taken to configure and monitor such huge machines.
One end-to-end Solution
frog’s collaboration allows for an end to end solution that streamlines all the processes under one platform and allows OEMs to monitor their machines and provide their customers with comprehensive analytics based data.